With shipments from China, and now Europe, slowed due to the spread of the coronavirus pandemic, keeping warehouses in the United States open and truckers employed has become a priority for B2B suppliers and buyers, logistics experts say.
Logistics services firms are setting in motion a mix of online and offline services designed to help carriers and independent truckers, as well as shippers, maintain operations while also minimizing risks related to the virus. FreightWise LLC, for example, is working with online sellers to manage shipments of more products more efficiently, and Next Trucking Inc. is listing on its online marketplace opportunities for carriers to return empty containers to a shipping port to help get the containers back to shippers.
Adding more products for online orders
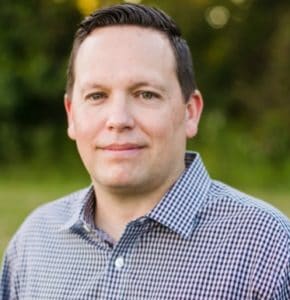
Chris Cochran, CEO, FreightWise
FreightWise is working with suppliers to include previously unlisted items, such as heavy or oversized equipment, in their online catalogs, and to calculate the shipping costs online. Purchases of heavy and oversized are typically made through a sales representative, who calculates the costs of shipping.
Other efforts focus on the basics of handling materials in warehouses in ways that support efficiency and risk management.
As B2B buyers encourage employees that can work from home to do so, some suppliers are experiencing a spike in online orders. That is prompting many suppliers to list all their products weighing more than 150 pounds or that are oversized in their catalog. Heavy and oversized items are typically shipped as LTL (less than truckload) freight, for which shipping costs can be difficult to calculate without the help of a sales representative, logistics experts say.
“The increasing shift to online sales during this period is putting pressure on suppliers to have their full catalog online,” says Chris Cochran, CEO of FreightWise, a Nashville-based logistics and transportation cost-management technology firm that provides shipping management services through a software-as-a-service platform.
A lot of heavy freight is not listed online due to the complexity of calculating shipping costs. “Our aim is to help suppliers make those products available to online buyers and provide shipping costs,” Cochran says.
Going with more parcel shipments
The loss of warehouse staff staying at home to self-quarantine after testing positive for the coronavirus, or staying home while awaiting test results, is creating a manpower shortage for some warehouse managers.
As a result, suppliers with understaffed warehouses are looking to simplify getting orders out the door, Cochran says. That means shipping all orders as parcel shipments, regardless of the cost. LTL freight is typically cheaper by the pound than parcel shipments.
FreightWise, which specializes in calculating LTL shipping costs, is enabling suppliers to calculate parcel shipping costs through its software apps.
Other efforts focus on the basics of handling of materials in warehouses in ways that support efficiency and risk management.
Setting safety standards
One of the biggest concerns for warehouse workers is preventing the spread of the coronavirus among themselves through the handling of packing materials used to bundle orders. Health officials have warned that the coronavirus can live on packing materials, such as cardboard.
That’s prompted warehouse managers to put more emphasis on ensuring that warehouse employees, especially those bundling shipments, are wearing proper protective clothing, such as vinyl gloves, and that workspaces within the warehouse are being disinfected.
“We’ve been talking to clients a lot about implementing safety standards in the warehouse to prevent the spread of the virus and keep employees productive,” Cochran says. “There are a lot of potentially (contaminated) materials that can come into the warehouse.”
Keeping freight clean and moving
To help its clients prevent the spread of the virus, FreightWise has developed a set of best practices that includes having workers wear protective clothing, such as vinyl gloves, face masks and protective suits. Other steps include recommending making hand sanitizers widely available and disinfecting work areas.
“This about taking steps to ensure workers can keep freight moving out of the warehouse,” says Cochran. “Keeping freight moving is critical to the economy.”
The effort to stem the spread of the virus is new territory for warehouse managers and Freightwise. “We’ve never seen these types of safety measures before in the warehouse,” Cochran says.
In some cases, the sanitary conditions inside warehouses are rivaling that of hospitals, Cochran adds.
Keeping truckers in business
Despite efforts to keep shipments moving through the warehouse, freight carriers are experiencing a downturn in shipments of products imported from China, which is just beginning to resume production after the virus began sweeping through the country last December.
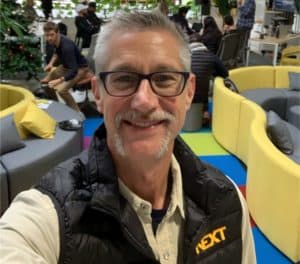
Bobby Napiltonia, chief revenue officer, Next Trucking
Container volumes from China into Los Angeles and Long Beach were off more than 30% since February, according to news reports. In addition, reports of blank sailings, or cargo ships scheduled to arrive, but that never do, have also increased.
“Shipments from China coming through Los Angeles and Long Beach account for a large portion of those ports’ volume,” says Bobby Napiltonia, chief revenue officer for Next Trucking, which operates an online portal that matches shippers with carriers and independent trucking owner-operators. “If the wait to move goods from China continues, even with ships from other parts of Asia and elsewhere still coming in, concerns are growing that it will cause some truckers to go out of business.”
Online listings of empty loads
To provide more opportunities for truckers to find work, Next Trucking has begun listing empty loads, which require the pick-up of an empty shipping container and returning it to port, on its online marketplace, NextTrucking.com.
Containers arriving from foreign countries must eventually be returned to their country of origin, either empty or full. While it can cost as much to transport an empty container overland as a full one, the backlog of empty containers that have shipped imports is growing rapidly, which creates an opportunity for truckers to keep working as suppliers need those containers back.
“With businesses and retailers starting to close down as a safety measure, the volume of empty containers being left after delivery is accumulating at an unprecedented rate,” Napiltonia says. “We are offering empty loads on our marketplace as a way to keep drivers on the road.”
Matching carriers and shippers
Next Trucking’s marketplace connects manufacturers and retailers with carriers based on a driver’s availability, load capacity and location. Shippers can see a shipment’s status in real time.
Nevertheless, as ports in New York and New Jersey begin to shut down as the spread of the coronavirus explodes there, concerns are increasing that truckers in that region will quickly become idled, which could drive many out of business.
During the first half of 2019, 640 freight companies closed their doors, more than for all of 2018, according to Broughton Capital, a transportation industry data firm.
“Truckers need loads to stay in business because they still have operating costs,” says Napiltonia. “When a gateway port or plant closes, it is no longer a source of shipments.”
Peter Lucas is a Highland Park, Illinois-based freelance journalist covering business and technology.
Sign up for a complimentary subscription to Digital Commerce 360 B2B News, published 4x/week, covering technology and business trends in the growing B2B ecommerce industry. Contact editor Paul Demery at [email protected] and follow him on Twitter @pdemery.
Follow us on LinkedIn and be the first to know when new Digital Commerce 360 B2B News content is published.