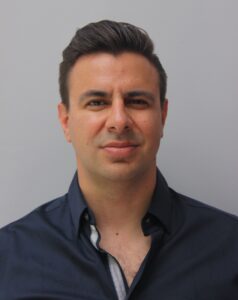
Costas Xyloyiannis
In recent years, ESG (environmental, social, governance) was hoisted to the top of the board agenda. To manage it, business leaders had to ensure that compliance and readiness across multiple areas were captured, analyzed and reported.
This job needed an owner. When it came time to delegate, leaders assessed whether a single department with a clear responsibility across all suppliers for all these areas existed. Unluckily, in most cases it did not. So, management turned to the next best option: procurement.
The function’s leaders, chief procurement officers (CPOs), now had new mandates to meet and quickly sought to apply technology. “Point” solutions, software dedicated to tackling individual use cases, were implemented. Often these tools were standalones. Integrating them with established P2P (purchase-to-pay) and S2P (source-to-pay) software suites, used to manage sourcing and supplier relationships, emerged as a challenge.
Today, swapping between these old and new tools is a slow and painful experience for procurement teams — and all their suppliers. The impact of this digital struggle extends even further, to the greater business. So, how does this stack up, and what can business leaders do about it?
Get to the heart of the problem
The digital environment which plagues procurement teams must also be navigated by suppliers. According to recent research, if a supplier wants to serve a single customer, they have to navigate around eight different tools, each with a unique login. The time loss to these, often smaller, businesses is a concern. Another is that behind each password, many of these solutions produce and then store data from suppliers using it.
So, the way in which each supplier works with the business results in their data being stored in an average of eight databases. Viewed as a whole, the supplier’s data is unreliable. It will be riddled with duplicates, gaps, errors and inconsistencies.
Now take this data pool scenario and multiply it by hundreds of thousands of suppliers. The millions or billions of entries that result in a murky view of supply chain activity. A consequence is that ESG reporting suffers. And so does the supplier relationship. Apart from the disjointed tech landscape, the experience suppliers have in communicating with procurement is also unsatisfactory, which for the most part stems from bad data.
All considered, can procurement teams really expect to receive the best work from suppliers? What about trustworthy data? If “no,” then how will the function progress? It has reached an evolutionary sticking point, and CPOs have a choice; they can accept things the way they are or find a way forward. Business executives can give their counterparts in procurement a hand, but first they should know the risks and rewards of progressing the function.
Resolve whether the reward is worth the risk
It’s one thing for management to see the problem for what it is, but deciding to address it cannot be taken lightly. Let’s start by envisioning what could be.
Encouragingly, a reality exists in which suppliers and procurement teams work together seamlessly, like partners in the same ecosystem. Suppliers are happy, their work is good, their data is pure. In this environment, procurement can thrive. Not only can the team deliver on traditional cost-saving metrics, but they can also generate accurate ESG reports. Further, the function is set up to contribute opportunities in areas that span the business — such as diversity and inclusion, sustainability and product innovation.
Behind this utopia, there is a movement which I like to think of as “supplier experience management.” As the name suggests, the idea is to manage an experience for suppliers, in which everyone is empowered to succeed — from the supplier base right through to the board.
As attractive as this environment is, the journey to reaching it is not easy or risk-free. The first challenge lies in people management: the entire business, from management to every employee, will have to reform how it views suppliers. Next, procurement will need to transform its digital setup. This transformation will require the CPO to radically rethink the architecture of the digital landscape, and then to embark on a rebuild. Expensive tools and teams will be needed to progress this plan, which raises the stakes. No doubt this is a momentous task.
But business leaders who refuse to stagnate won’t be alone. Many enterprises have transformed the status quo and are enjoying the fruits. For example, in 2013 an early adopter, BAE Systems, started to manage supplier experience. This led their procurement team to remove process friction for suppliers and enabled them to consolidate data from 50,000 suppliers across North American. The resulting “single source of truth” was incredibly valuable to the broader business in 2020 when COVID-19 hit. When leaders needed it most, they could access a clear and accurate view of the supply chain. This visibility, coupled with the zero-friction supplier environment they had established, meant that every department could respond to the crisis with agility.
The benefits of the agility gained through supplier experience are being enjoyed by many other companies, including the likes of Mondelēz International, Baker Hughes, Lenovo, and more. A wave of globally recognized CPG brands such as Unilever, Mars and Heineken have also joined the supplier-centric movement in the last 18 months.
Take inspiration from the pioneers and drive change
Trailblazers of the supplier experience principle follow a proven method. Four steps stand out, by which the broader business, procurement and all suppliers can achieve mutual success. For business leaders to reach this point, here’s a plan of action:
- First, work with the CPO to assemble a legion of loyal leaders. Their support will be invaluable. Attaining it, however, might push your persuasion skills. Some executives, particularly those who still view procurement a transaction center, will resist working with suppliers beyond the boundaries of cost savings. So, show them the value. Look at the virtues of “experience” management in other areas, such as with employees and customers. Can parallels be drawn to suppliers? Showcase the woes of a fractious supplier environment. What risks arise? Were major opportunities missed? Explore what a more harmonious setting will yield.
- Next, with the c-suite on board, it’s time to gain ground. The key move is to abolish 100% of the barrier to supplier success: friction. Before that, you need to know what all the process pain points are. Unearthing these insights will require curiosity. What do these obstacles look like to suppliers? How are they removed? Getting immersed in their world — caring, stepping into their shoes, doing surveys — is key.
- Now from this vantage point, work with procurement to craft a friction-free digital environment. Other pioneers follow a data-first approach, in which a central platform is used to consolidate, host and govern all supplier data. Once the landscape is engineered to prioritise master data, procurement can automate. Apply routines for transactional jobs and then use the saved time to introduce digital workflows that make the supplier experience even better
Finish strong
At this stage, the business has helped procurement to digitally transform. In doing so, the function — and the business — have gained two assets: a single source of truth in supplier data and a supplier network whose needs are better met.
It would be easy to stop at this point, but a crucial step remains. The supplier experience which has taken so much to improve, must be maintained. For this maintenance, we need human collaboration. Everyone who engages suppliers (most of the company) must view them as equal, valued partners in a shared ecosystem — and treat them as such.
With both interpersonal and operational barriers removed, the business can partner with all its suppliers. In this scenario suppliers are happier, and procurement can deliver its mandates, the benefits of which extend well into the business.
About the author
Costas Xyloyiannis is co-founder and CEO of HICX, a supplier experience management platform.
Sign up
Sign up for a complimentary subscription to Digital Commerce 360 B2B News, published 4x/week. It covers technology and business trends in the growing B2B ecommerce industry. Contact editor Paul Demery at paul@digitalcommerce360.com and follow him on Twitter @pdemery.
Follow us on LinkedIn and be the first to know when new Digital Commerce 360 B2B News content is published.
Favorite